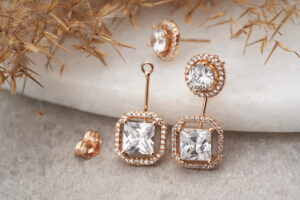
The enduring allure of diamonds lies not only in their brilliance but also in their unparalleled durability. Natural diamonds have long been regarded as the hardest substance known to man, capable of withstanding wear and tear that would erode most other materials. However, the rise of artificial diamonds, while introducing remarkable advancements, has also brought to the forefront certain durability challenges in comparison to their natural counterparts. Natural diamonds, with their extraordinary hardness, have been revered for their resistance to abrasion and wear. This exceptional durability has made them the preferred choice in various industrial applications, from cutting and grinding to drilling and polishing. Natural diamonds’ ability to maintain their integrity under extreme pressure and heat conditions has been pivotal in their widespread use. On the other hand, artificial diamonds, also known as lab-grown or synthetic diamonds, are created through controlled processes that replicate the conditions under which natural diamonds form deep within the Earth. These man-made diamonds are celebrated for their many attributes, such as precision cutting and sharpness, as discussed in the previous essay. However, when it comes to overall durability, they may face some challenges when compared to natural diamonds.
One of the key factors influencing the durability of artificial diamonds is their growth method. High-pressure, high-temperature (HPHT) and chemical vapor deposition (CVD) are the two primary processes used to produce synthetic diamonds. While these methods can yield diamonds with exceptional hardness, they may also introduce certain weaknesses or vulnerabilities not found in natural diamonds. For instance, artificial diamonds may exhibit variations in crystal structure, internal stress, or the presence of impurities that affect their overall durability. These variations can make synthetic diamonds more susceptible to fracture or cleavage under extreme conditions, particularly when used in heavy-duty industrial applications. The brittleness of some artificial diamonds can be a limitation in certain cutting or grinding processes that require consistent durability. However, it is important to note that the durability challenges associated with artificial diamonds are not insurmountable. Ongoing research and development efforts are focused on enhancing the structural integrity of lab-grown diamonds, making them more resistant to external forces and wear. Manufacturers are continually refining the growth processes to reduce the likelihood of internal defects and inconsistencies. Moreover, for many applications where synthetic diamonds are used, the challenges related to durability are mitigated by the precision, sharpness, and cost-effectiveness they offer. In instances where extreme hardness is not the primary requirement, the versatility of artificial diamonds makes them a highly valuable choice. In fact, some industries value the controlled and predictable characteristics of synthetic diamonds, as they can be tailored to specific needs.
In conclusion, the evolution of artificial diamonds has brought about both advantages and challenges in terms of durability. While natural diamonds remain the standard for extreme hardness and resistance to wear, artificial diamonds offer an array of benefits, particularly in precision cutting and sharpening tools. The ongoing efforts to address durability challenges in synthetic diamonds are a testament to the industry’s commitment to refining and expanding the applications of these remarkable gemstones.